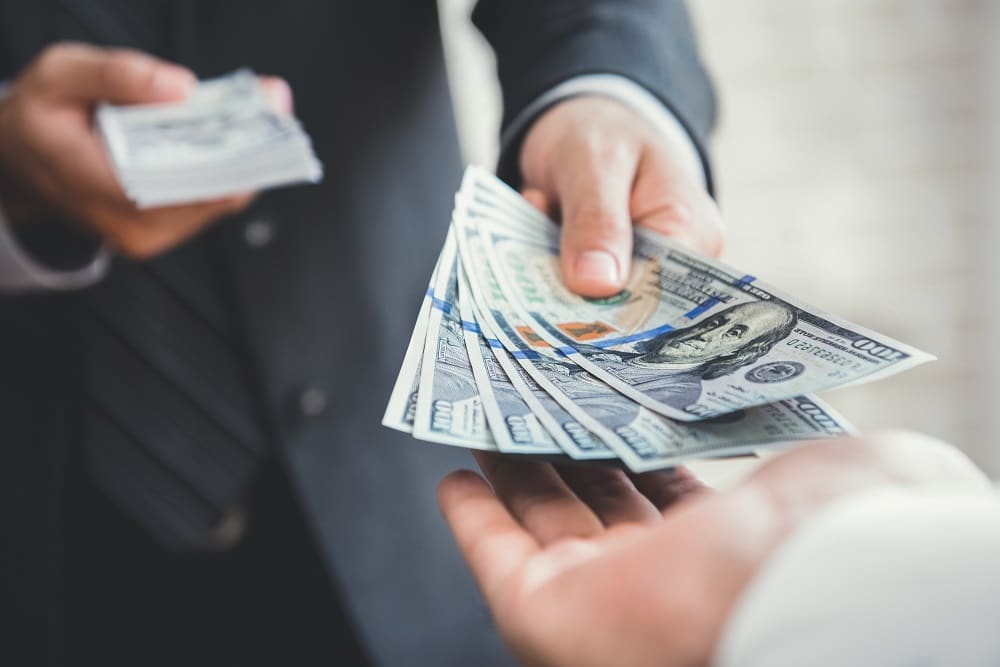
It was a snowy day in early March when Ruth Joad pranged her car. The one-year-old Volkswagen needed a new bumper and sensors. Her insurer, Aviva, told her to book it into an approved dealership – and that’s where it’s been ever since.
“Four months on, there’s still no update on when they’ll have the bumper,” she says. “It took three months for Aviva to get me a courtesy car, and when I call for updates I’m sent round in circles.”
Late last week, after queries from the Observer, Aviva said the part had finally arrived and her repair had been prioritised. The company apologised and paid compensation.
Joad is one of thousands of drivers left in limbo because of a global shortage of car parts. Insurers are writing off vehicles because of indefinite repair delays, according to the National Body Repair Association, which estimates that drivers are having to wait five weeks longer than the pre-pandemic average to book cars in.
Several who have contacted the Observer have been forced off the road for months with no update on when their vehicle can be repaired. A shortage of courtesy cars, caused by the same manufacturing issues, means those in rural areas are effectively immobilised.
Car manufacturers blame Covid and the invasion of Ukraine for disrupting global supply chains. Two-thirds of vehicle components are produced in China and the Middle East, where lockdowns hit supply and demand, while Ukraine is critical in the manufacture of semiconductors. Added to this, there’s a Europe-wide shortage of mechanics and HGV drivers to install and transport the parts.
However, our investigation suggests some drivers are being fobbed off by manufacturers who are prioritising sales over repairs. Several readers who had waited months because a crucial part could not be sourced found it could be summoned as soon as we questioned the delays.
Mark Ellis was left with an unroadworthy Mercedes for seven months after a headlamp unit failed, leaving him without lights or indicators. “The dealer ordered a replacement last October and, come May, could give me no date on when it might become available,” he says. “Raising a complaint to Mercedes-Benz UK customer services yielded no response. Without lights, it couldn’t pass its MOT.”
Ellis’s car was repaired a week after the Observer intervened. Mercedes blamed “global supply issues”.
Anitre MacDonagh’s Jeep Compass was also stranded when a replacement for a defective oil part could not be sourced. “After five weeks, the dealer notified us that there was a production problem and our order had been cancelled,” she says.
“According to Fiat UK [Jeep’s parent company], the manufacturer needed an order of 200 parts before it could be produced, and it could take up to a year. We called Fiat/Jeep dealers in the US, Italy and Albania on the off chance it might be in stock, but no such luck. One dealer told us Fiat has stopped making replacement parts, meaning our four-year-old is now obsolete.”
Fiat produced the part as soon as we got in touch. It tells us: “Due to an unfortunate set of circumstances, there has, on this occasion, been an error in the process of obtaining the part for the customer.”
Clara Coleman* was left without wheels after her BMW was recalled by the manufacturer to investigate a software issue. She was informed that a cooling device was leaking and, as a necessary part was unavailable, the repair could take months.
“The dealer advised they would need to impound the car until it could be repaired as the fault could be fatal. However, they could not offer a courtesy car,” she says. “In the meantime, I am paying my finance agreement with BMW for a car which has been condemned, and no end in sight.”
The part was found and a loan vehicle provided two days after the Observer made inquiries. BMW says: “The parts required are not on back order. Rather, they had to be ordered from a central UK warehouse. BMW, and its retail network, always strive to minimise disruption for our customers, offering mobility solutions on a case-by-case basis.”
According to Chris Rosamond, current affairs and features editor of car magazine Auto Express, poor communications on the part of manufacturers, and a drive to boost sales at the expense of repairs, are leaving thousands of drivers stranded.
“In recent months parts shortages have caused manufacturers to prioritise new vehicle production, and they are choosing to ringfence parts supply or production capacity for that purpose,” he explains. “The knock-on effect has been frustration and uncertainty, often not helped by a less-than-transparent approach from manufacturers when it comes to sharing information via dealers.”
It’s horrendous … manufacturers use available spare parts to put into new cars, as that is where the money is Senior executive in body repair sector
Industry insiders claim the situation is the worst they’ve ever seen. “It’s horrendous,” says one senior executive in the body repair sector, who asked not to be named.
“Every manufacturer is affected by the current shortage of semiconductor chips. Because car production dropped during the pandemic, manufacturers cut back orders for spare parts. Meanwhile, demand for electronic devices in the home soared, so chip producers started selling more to Apple and the like.
“Now manufacturers find themselves at the back of the queue and, once they get hold of chips, they use available spare parts to put into new cars, as that’s where the money is.”
He says insurance firms are increasingly writing off vehicles with minor damage because it’s cheaper than funding a courtesy car during an indefinite wait. It’s the consumer who ultimately foots the bill. The average premium has risen 40% in 12 months, according to new research by Confused.com. An increase in payouts for write-offs is one of the factors it cites for the record price rise.
The Association of British Insurers tells the Observer: “Like many other sectors, motor insurers are facing significant challenges due to inflation, supply-chain disruption and global shortages, and are doing all they can to manage the impact.
“Whether a damaged car can be repaired, or written off, will be reviewed on a case-by-case basis.”
There is no legal requirement for spares to be available for a set period in the UK, but all large manufacturers have signed up to The Motor Ombudsman’s new car code, which makes the vague stipulation that parts should be available throughout production of a model and “for a reasonable period thereafter”.
If a car is less than two years old, or it is under warranty, the manufacturer has a legal responsibility to replace it with a similar spec if it can’t be repaired.
*Name has been changed
How to beat the delays
Repairs under warranty, or via an insurance claim, have to be undertaken by a dealer or an approved garage. Drivers of older vehicles needing routine work may be better off seeking an independent body workshop and authorising the use of non-branded parts or components recycled from compatible vehicles. The one positive of the strangled supply chain is that the sale of these so-called “green parts” is soaring in response to the manufacturing shortfall, and some insurance companies are starting to embrace them as an alternative. They are up to 70% cheaper than new components and reduce the environmental impact of the repair industry.